Removing & Installing Cam Bearings
Author: Josh Brown Date Posted:1 October 2017
The cam bearings in engines are removed and installed when doing a complete engine rebuild.
Begin by stripping down the engine. Once all parts are removed, the cam bearings can be taken out, this will help to remove any dust or dried grease that may be caught behind the bearings.
Next, ensure the motor is clean and prepared for assembly. (For a detailed guide on how to do this properly, see our piece on "ENGINE CLEANING")
When removing and installing the cam bearings, there are two different tools you can use; "fixed' or "expandable".
Fixed tools are designed specifically to fit ONE size of bearing. Expandable tools, as their name suggests, are multi-purpose, and can be used on a multiple of bearing sizes.
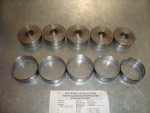
WE RECOMMEND FIXED!
With FIXED, you are guaranteed precise alignment.*
A FIXED tool won't slip and damage the cam bearing.
An EXPANDABLE tool may be used if that's all you have, but just be aware that this leaves much more room for error, and potential damage to cam bearings.
Some cam bearings have to be aligned with oil gallery holes, which is critical for the supply of oil to the crankshaft. I find marking cam bearings (with a permanent marker) where the oil hole should be, makes it easier to align.
Aligning a hole PERFECTLY is possible...but hard to achieve. When you are preparing for this, ensure that at least 3/4 of the hole is showing.
It is NOT good practice to install a new cam bearing, misalign the hole, and have to remove and re-install it as this can cause a whole size or more to be accidentally shaved off the cam bearing.
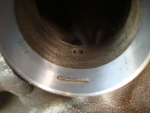
Aligning cam gap with oil hole.
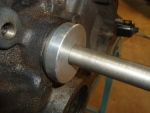
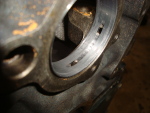
If the oil gallery holes are still slightly off, a drill bit can expand it.
NB/ If you do this, remember to DEBURR the cam bearing oil hole once you've drilled it.
The final test is to install the camshaft and ensure it rotates freely.
An old-school method used when camshafts appeared stuck, or wouldn't rotate freely, involved the builder taking a blunt chisel and hammer, and hitting down hard on the core shaft, even spaces apart.
While this spreads the distance between the high spots on the camshaft, and does allow it to turn more freely, it also adds the possibility of bending the camshaft, giving you more problems in the future.